.
Turbo Engine
- This article describes the internal combustion engine component often known as a turbo. For other meanings of turbo, see turbo (disambiguation).
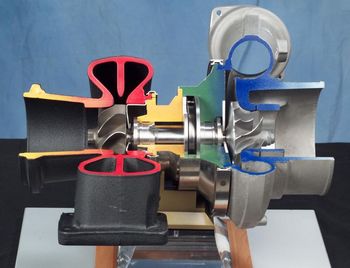
A turbocharger is an exhaust gas-driven compressor used to increase the power output of an internal-combustion engine by increasing the mass of oxygen entering the engine. A key advantage of turbochargers is that they offer a considerable increase in engine power with only a slight increase in weight.
Principle of operation
A turbocharger is an exhaust gas driven Supercharger. Turbochargers are a true gas compressor, as the gas (air) is compressed inside of the turbocharger. Unlike a Roots Blower, which is an air mover and does not actually compress air. Engines with a Roots Blower have a higher boost level as a result of the blower moving more air than a naturally aspirated engine normally uses, thus more air is packed into the engine and boost is created.
A turbocharger has two main parts. The compressor and the turbine. The exhaust gasses from the engine are directed to the turbine wheel, which takes the enthalpy (energy) of the exhaust and converts that energy into rotating energy. This motion rotates a shaft that both the compressor wheel and the turbine wheel are attached to. This spinning motion spins the compressor wheel, which then compresses the air from the intake air above atmospheric pressure, greatly increasing the volumetric efficiency beyond that of naturally-aspirated engines. The exhaust gasses either hit the turbine wheel, or are directed around the turbine wheel by wastegate. Exhaust gas directed through the wastegate is not used to spin the shaft assembly. This is done to limit the amount of power available to drive the compressor wheel, which is used to limit the boost level of the turbo.
The term supercharger is very often used when referring to a mechanically driven supercharger, which is most often driven from the engine's crankshaft by means of a belt (otherwise, and in many aircraft engines, by a geartrain), whereas a turbocharger is exhaust-driven, the name turbocharger being a contraction of the earlier "turbosupercharger". Because the turbine of a turbocharger is in-itself a heat engine, a turbocharger equipped engine will normally compress the intake air more efficiently than a mechanical supercharger. Turbo Lag is the delayed response of the engine that is due to the compressor coming up to a speed where boost levels are attained. Engines with mechanical superchargers are typically more responsive initially. Because turbochargers are nearly twice as efficient at other methods of supercharging, the "turbo lag" is negligible. Technology in turbocharging has come to the point where turbocharged engines make boost nearly as quickly as mechanically driven superchargers.
The compressor increases the pressure of the air entering the engine, so a greater mass of oxygen enters the combustion chamber in the same time interval (an increase in fuel is required to keep the mixture the same air to fuel ratio). This greatly improves the volumetric efficiency of the engine, and thereby creates more power. The additional fuel is provided by the proper tuning of the fuel injectors or carburetor.
The increase in pressure is called "boost" and is measured in pascals, bars or lbf/in². The energy from the extra fuel leads to more overall engine power. For example, at 100% efficiency a turbocharger providing 101 kPa (14.7 lbf/in²) of boost would effectively double the amount of air entering the engine because the total pressure is twice atmospheric pressure. However, there are some parasitic losses due to heat, friction from bearings, aerodynamic drag from the compressor wheel, and exhaust backpressure from the turbine. Turbochargers are typically 70-85% efficient, at peak efficiency, due to having to heat the air during the compression. Turbochargers (centrifugal superchargers) are the most efficient superchargers because they take the least amount of energy to spin the wheels, and they heat the incoming air less than other styles of superchargers like the Roots and the Lysholm blower.
For most street driven engines that are limited to using gasoline that is publically available, boost levels typically range from 10psig to 18 psig, but the levels can be more depending upon particular setups. Because it is a centrifugal pump, a typical turbocharger, depending on design, will only start to deliver boost from a certain RPM where the engine starts producing enough exhaust gas to spin the turbocharger fast enough to make boost. This engine RPM is referred to as the boost threshold. Another fact to observe is that the relation between boost pressure and compressor RPM is somewhat exponential, and the relation between compressor rpm and airflow is very small. A turbocharger that is pushing 15 psi when the engine is at 3000 rpm will only have increased a little bit in speed when maintaining the same pressure at 6000 engine RPM; given that it is still within the design limits of the compressor. For this very same reason, belt-driven centrifugal superchargers have a very narrow power band and deliver max boost only when the engine is at max RPM.
In the past, engines had to have lower compression to be able to effectively use the boost pressure from the turbocharger. This was done to limit detonation. With the technology available now, practically any naturally aspirated engine can benefit from turbocharging. The levels of power that can be attained are limited by the gasoline octane available. One way to get more power out of turbocharged engines that are limited to using low (<93 octane) fuels, is to lower the compression ratio. This allows you to run more boost, with increased the power levels. Engines can be specifically designed to operate with a turbocharger, but nearly any engine can benefit with the use of a turbocharger. During operation at high altitudes, such as with airplanes, the power recovery of a turbocharger makes a big difference to total power output of both engine types. This factor makes turbocharging aircraft engines considerably advantageous. The first applications for turbocharging were used on Diesel Powered ships and Locomotives, long before they were used in Aircraft.
A main disadvantage of high boost pressures for internal combustion engines is that compressing the inlet air increases its temperature. This increase in charge temperature is a limiting factor for petrol engines that can only tolerate a limited increase in charge temperature before detonation occurs. The higher temperature is a volumetric efficiency downgrade for both types of engine. The pumping-effect heating can be alleviated by aftercooling (sometimes called intercooling).
Fuel efficiency
Since a turbocharger increases the specific horsepower output of an engine, the engine will also produce increased amounts of waste heat. This can sometimes be a problem when fitting a turbocharger to a car that was not designed to cope with high heat loads. This extra waste heat combined with the lower compression ratio (more specifically, expansion ratio) of turbocharged engines contributes to slightly lower thermal efficiency, which has a small but direct impact on overall fuel efficiency.
It is another form of cooling that has the largest impact on fuel efficiency: charge cooling. Even with the benefits of intercooling, the total compression in the combustion chamber is greater than that in a naturally aspirated engine. To avoid knock while still extracting maximum power from the engine, it is common practice to introduce extra fuel into the charge for the sole purpose of cooling. While this seems counterintuitive, this fuel is not burned. Instead, it absorbs and carries away heat when it changes phase from liquid to gas. Also, because it is more dense than the other inert substance in the combustion chamber, nitrogen, it has a higher specific heat and more heat capacitance. It "holds" this heat until it is released in the exhaust stream, preventing destructive knock. This thermodynamic property allows manufacturers to achieve good power output with common pump fuel at the expense of fuel economy and emissions.
Lastly, the efficiency of the turbocharger itself can have an impact on fuel efficiency. Using a small turbocharger will give good response and low lag at low to mid RPMs, but can choke the engine on the exhaust side and generate huge amounts of pumping-related heat on the intake side as RPMs rise. A large turbocharger will be very efficient at high RPMs, but is not a realistic application for a street driven automobile. Variable vane and ball bearing technologies can make a turbo more efficient across a wider operating range, but tend to be too expensive to incorporate into mass produced vehicles.
The engine management systems of most modern vehicles can control boost and fuel delivery according to charge temperature, fuel quality and altitude, among other factors. Some systems are more sophisticated and aim to even more precisely deliver fuel based on combustion quality. For example, the Trionic-7 system from SAAB provides immediate feedback on the combustion while it is occuring using an electrical charge.
The new 2.0L FSI turbo engine from VW/Audi incorporates lean burn and direct injection technology to conserve fuel under low load conditions. It is a very complex system that involves many moving parts and sensors in order to manage airflow characteristics inside the chamber itself, allowing it to use a stratified charge with excellent atomization. The direct injection also has a tremendous charge cooling effect enabling this engine to use a higher compression ratio and boost pressures than a typical port-injection turbo engine.
Design details
When a gas is compressed, its temperature rises. It is not uncommon for a turbocharger to be pushing out air that is 90°C (200°F). Compressed air from a turbo may be (and most commonly is, on petrol engines) cooled before it is fed into the cylinders, using an intercooler or a charge air cooler (a heat-exchange device).
A turbo spins very fast; most peak between 80,000 and 150,000 rpm (using low inertia turbos, 190,000 rpm) depending on size, weight of the rotating parts, boost pressure developed and compressor design. Such high rotation speeds would cause problems for standard ball bearings leading to failure so most turbo-chargers use fluid bearings. These feature a flowing layer of oil that suspends and cools the moving parts. The oil is usually taken from the engine-oil circuit and usually needs to be cooled by an oil cooler before it circulates through the engine. Some turbochargers use incredibly precise ball bearings that offer less friction than a fluid bearing but these are also suspended in fluid-dampened cavities. Lower friction means the turbo shaft can be made of lighter materials, reducing so-called turbo lag or boost lag. Some car makers use water cooled turbochargers for added bearing life.
Turbochargers with foil bearings are in development which eliminates the need for bearing cooling or oil delivery systems, thereby eliminating the most common cause of failure, while also significantly reducing turbo lag.
To manage the upper-deck air pressure, the turbocharger's exhaust gas flow is regulated with a wastegate that bypasses excess exhaust gas entering the turbocharger's turbine. This regulates the rotational speed of the turbine and the output of the compressor. The wastegate is opened and closed by the compressed air from turbo (the upper-deck pressure) and can be raised by using a solenoid to regulate the pressure fed to the wastegate membrane. This solenoid can be controlled by Automatic Performance Control, the engine's electronic control unit or an after market boost control computer. Another method of raising the boost pressure is through the use of check and bleed valves to keep the pressure at the membrane lower than the pressure within the system.
Some turbochargers (normally called variable geometry turbochargers) utilise a set of vanes in the exhaust housing to maintain a constant gas velocity across the turbine, the same kind of control as used on power plant turbines. These turbochargers have minimal amount of lag, have a low boost threshold, and are very efficient at higher engine speeds. In many setups these turbos don't even need a wastegate. The vanes are controlled by a membrane identical to the one on a wastegate but the level of control required is a bit different. The first production car to use these turbos was the limited-production 1989 Shelby CSX-VNT, equipped with a 2.2L petrol engine. The Shelby CSX-VNT utilised a turbo from Garrett, called the VNT-25 because it uses the same compressor and shaft as the more common Garrett T-25. This type of turbine is called a Variable Nozzle Turbine (VNT). Turbocharger manufacturer Aerocharger uses the term 'Variable Area Turbine Nozzle' (VATN) to describe this type of turbine nozzle. Other common terms include Variable Turbine Geometry (VTG), Variable Geometry Turbo (VGT) and Variable Vane Turbine (VVT).
The 2006 Porsche 911 Turbo has a twin turbocharged 3.6-litre flat six, and the turbos used are BorgWarner's Variable Geometry Turbos (VGTs) . This is significant because although VTGs have been used on advanced diesel engines for a few years and on the Shelby CSX-VNT, this is the first time the technology has been implemented on a high production petrol car (only 500 Shelby CSX-VNTs were ever produced) . This is because in petrol cars exhaust temperatures are much higher (than in diesel cars), and this normally has adverse effects on the delicate, moveable vanes of the turbo, Porsche engineers however have managed to combat this problem with the new 911 Turbo.
Reliability
As long as the oil supply is clean and the exhaust gas does not become overheated (lean mixtures or retarded spark timing on a gasoline engine) a turbocharger can be very reliable but care of the unit is important. Replacing a turbo that lets go and sheds its blades will be expensive. The use of synthetic oils is recommended in turbo engines.
After high speed operation of the engine it is important to let the engine run at idle speed for around one to three minutes before turning off the engine. For example Saab, in its owner manuals, recommends a period of just 30 seconds. This lets the turbo rotating assembly cool from the lower exhaust gas temperatures. Not doing this will also result in the critical oil supply to the turbocharger being severed when the engine stops while the turbine housing and exhaust manifold are still very hot, leading to coking of the lubricating oil trapped in the unit when the heat soaks into the bearings and later, failure of the supply of oil when the engine is next started causing rapid bearing wear and failure. Even small particles of burnt oil will accumulate and lead to choking the oil supply and failure. A turbo timer is a device designed to keep an automotive engine running for a pre-specified period of time, in order to execute this cool-down period automatically. Oil coking is completely eliminated by foil bearings. You can also buy a turbo timer with a temperature sensor at [www.pampeperformance.com], so it idles longer than normal when it's hotter than normal.
A more complex and problematic protective barrier against oil coking is the use of watercooled bearing cartridges. The water boils in the cartridge when the engine is shut off and forms a natural recirculation to drain away the heat. It is still a good idea to not shut the engine off while the turbo and manifold are still glowing.
In custom applications utilising tubular headers rather than cast iron manifolds, the need for a cooldown period is reduced because the lighter headers store much less heat than heavy cast iron manifolds.
Diesel engines are usually much kinder to turbos because their exhaust gas temperature is much lower than that of gasoline engines and because most operators allow the engine to idle and do not switch it off immediately after heavy use.
Lag
A lag is sometimes felt by the driver of a turbocharged vehicle as a delay between pushing on the accelerator pedal and feeling the turbo kick-in. This is symptomatic of the time taken for the exhaust system driving the turbine to come to high pressure and for the turbine rotor to overcome its rotational inertia and reach the speed necessary to supply boost pressure. The directly-driven compressor in a positive-displacement supercharger does not suffer this problem. (Centrifugal superchargers do not build boost at low RPMs like a positive displacement supercharger will). Conversely on light loads or at low RPM a turbocharger supplies less boost and the engine is more efficient than a supercharged engine.
Lag can be reduced by lowering the rotational inertia of the turbine, for example by using lighter parts to allow the spool-up to happen more quickly. Ceramic turbines are a big help in this direction. Unfortunately, their relative fragility limits the maximum boost they can supply. Another way to reduce lag is to change the aspect ratio of the turbine by reducing the diameter and increasing the gas-flow path-length. Increasing the upper-deck air pressure and improving the wastegate response helps but there are cost increases and reliability disadvantages that car manufacturers are not happy about. Lag is also reduced by using a foil bearing rather than a conventional oil bearing. This reduces friction and contributes to faster acceleration of the turbo's rotating assembly.
Another common method of equalizing turbo lag, is to have the turbine wheel "clipped", or to reduce the surface area of the turbine wheel's rotating blades. By clipping a minute portion off the tip of each blade of the turbine wheel, less restriction is imposed upon the escaping exhaust gases. This imparts less impedance onto the flow of exhaust gasses at low RPM, allowing the vehicle to retain more of its low-end torque, but also pushes the effective boost RPM to a slightly higher level. The amount a turbine wheel is and can be clipped is highly application-specific. Turbine clipping is measured and specified in degrees.
Other setups, most notably in V-type engines, utilize two identically-sized but smaller turbos, each fed by a separate set of exhaust streams from the engine. The two smaller turbos produce the same (or more) aggregate amount of boost as a larger single turbo, but since they are smaller they reach their optimal RPM, and thus optimal boost delivery, faster. Such an arrangement of turbos is typically referred to as a parallel twin-turbo system.
Some car makers combat lag by using two small turbos (like Toyota, Subaru, Maserati, Mazda, and Audi). A typical arrangement for this is to have one turbo active across the entire rev range of the engine and one coming on-line at higher RPM. Early designs would have one turbocharger active up to a certain RPM, after which both turbochargers are active. Below this RPM, both exhaust and air inlet of the secondary turbo are closed . Being individually smaller they do not suffer from excessive lag and having the second turbo operating at a higher RPM range allows it to get to full rotational speed before it is required. Such combinations are referred to as a sequential twin-turbo. Sequential twin-turbos are usually much more complicated than a single or parallel twin-turbo systems because they require what amounts to three sets of pipes-intake and wastegate pipes for the two turbochargers as well as valves to control the direction of the exhaust gases. An example of this is the current BMW E60 5-Series 535d. Many new diesel engines use this technology to not only eliminate lag but also to reduce fuel consumption and produce cleaner emissions.
Lag is not to be confused with the boost threshold; however, many publications still make this basic mistake. The boost threshold of a turbo system describes the minimum turbo RPM at which the turbo is physically able to supply the requested boost level. Newer turbocharger and engine developments have caused boost thresholds to steadily decline to where day-to-day use feels perfectly natural. Putting your foot down at 1200 engine RPM and having no boost until 2000 engine RPM is an example of boost threshold and not lag.
Race cars often utilise anti-lag to completely eliminate lag at the cost of reduced turbocharger life.
On modern diesel engines, this problem is virtually eliminated by utilising a variable geometry turbocharger.
Boost
Boost refers to the increased manifold pressure that is generated by the intake side turbine. This is limited to keep the turbo inside its design operating range by controlling the wastegate which shunts the exhaust gases away from the exhaust side turbine. Many diesel engines do not have any wastegate because the amount of exhaust energy is controlled directly by the amount of fuel injected into the engine, and slight variations in boost pressure do not make a difference for the engine.
Applications
Turbocharging is very common on diesel engines in conventional automobiles, in trucks, locomotives, for marine and heavy machinery applications. In fact, for current automotive applications, non-turbocharged diesel engines are becoming increasingly rare. Diesels are particularly suitable for turbocharging for several reasons:
- Naturally-aspirated diesels have lower power-to-weight ratios compared to gasoline engines; turbocharging will improve this P:W ratio.
- Diesel engines require more robust construction because they already run at very high compression ratio and at high temperatures so they generally require little additional reinforcement to be able to cope with the addition of the turbocharger. Gasoline engines often require extensive modification for turbocharging.
- Diesel engines have a narrower band of engine speeds at which they operate, thus making the operating characteristics of the turbocharger over that "rev range" less of a compromise than on a gasoline-powered engine.
- Diesel engines blow nothing but air into the cylinders during cylinder charging, squirting fuel into the cylinder only after the intake valve has closed and compression has begun. Gasoline/petrol engines differ from this in that both fuel and air are introduced during the intake cycle and both are compressed during the compression cycle. The higher intake charge temperatures of forced-induction engines reduces the amount of compression that is possible with a gasoline/petrol engine, whereas diesel engines are far less sensitive to this.
Today, turbocharging is most commonly used on two types of engines: Gasoline engines in high-performance automobiles and diesel engines in transportation and other industrial equipment. Small cars in particular benefit from this technology, as there is often little room to fit a larger-output (and physically larger) engine. Saab has been the leading car maker using turbochargers in production cars, starting with the 1978 Saab 99. The Porsche 944 utilized a turbo unit in the 944 Turbo (Porsche internal model number 951), to great advantage, bringing its 0-100 km/h (0-60 mph) times very close to its contemporary non-turbo "big brother", the Porsche 928. Contemporary examples of turbocharged performance cars include the Renault R5 Turbo,Ford Mustang SVO, Peugeot 205 T16, Audi TT, Fiat Coupe 20vt, Buick Regal Grand National, Dodge SRT-4, Subaru Impreza WRX, Mazda RX-7, Mitsubishi Lancer Evolution, Nissan Skyline GT-R, Toyota Supra RZ, and the Porsche 911 Turbo.
Small car turbos are increasingly being used as the basis for small jet engines used for flying model aircraft—though the conversion is a highly specialised job—one not without its dangers.
Most modern turbocharged aircraft use an adjustable wastegate. The wastegate is controlled manually, or by a pneumatic/hydraulic control system, or, as is becoming more and more common, by a flight computer. In the interests of engine longevity, the wastegate is usually kept open, or nearly so, at sea-level to keep from overboosting the engine. As the aircraft climbs, the wastegate is gradually closed, maintaining the manifold pressure at or above sea-level. In aftermarket applications, aircraft turbochargers sometimes do not overboost the engine, but rather compress ambient air to sea-level pressure. For this reason, such aircraft are sometimes referred to as being turbo-normalised. Most applications produced by the major manufacturers (Beech, Cessna, Piper and others) increase the maximum engine intake air pressure by as much as 35%. Special attention to engine cooling and component strength is required because of the increased combustion heat and power.
Turbo-Alternatorturbo_alternators/default.asp is a form of turbocharger that generates electricity instead of boosting engine's air flow. On September 21 2005, Foresight Vehicle announced the first known implementation of such unit for automobiles, under the name TIGERS (Turbo-generator Integrated Gas Energy Recovery System).[1]
History
The turbocharger was invented by Swiss engineer Alfred Buchi, who had been working on steam turbines. His patent for the internal combustion turbocharger was applied for in 1905. Diesel ships and locomotives with turbochargers began appearing in the 1920s.
One of the first applications of a turbocharger to a non-Diesel engine came when General Electric engineer, Sanford Moss attached a turbo to a V12 Liberty aircraft engine. The engine was tested at Pike's Peak in Colorado at 14,000 feet to demonstrate that it could eliminate the power losses usually experienced in internal combustion engines as a result of altitude.
Turbochargers were first used in production aircraft engines in the 1930s prior to World War II. The primary purpose behind most aircraft-based applications was to increase the altitude at which the airplane can fly, by compensating for the lower atmospheric pressure present at high altitude. Aircraft such as the Lockheed P-38 Lightning, Boeing B-17 Flying Fortress and B-29 Superfortress all used exhaust driven "turbo-superchargers" to increase high altitude engine power. It is important to note that turbosupercharged aircraft engines actually utilized a gear-driven centrifugal type supercharger in series with a turbocharger.
Turbo-Diesel trucks were produced in Europe and the United States (notably by Cummins) after 1949. The turbocharger hit the automobile world in 1952 when Fred Agabashian qualified for pole position at the Indianapolis 500 and led for 100 miles before tire shards disabled the blower.
The first production turbocharged automobile engines came from General Motors. The A-body Oldsmobile Cutlass Jetfire and Chevrolet Corvair Monza Spyder were both fitted with turbochargers in 1962. The Oldsmobile is often recognized as the first, since it came out a few months earlier than the Corvair. Its Turbo Jetfire was a 215 in³ (3.5 L) V8, while the Corvair engine was either a 145 in³ (2.3 L)(1962-63) or a 164 in³ (2.7 L) (1964-66) flat-6. Both of these engines were abandoned within a few years, and GM's next turbo engine came more than ten years later.
Offenhauser's turbocharged engines returned to Indianapolis in 1966, with victories coming in 1968. The Offy turbo peaked at over 1,000 hp in 1973, while Porsche dominated the Can-Am series with a 1100 hp 917/30. Turbocharged cars dominated the Le Mans between 1976 and 1994.
BMW led the resurgence of the automobile turbo with the 1973 2002 Turbo, with Porsche following with the 911 Turbo, introduced at the 1974 Paris Motor Show. Buick was the first GM division to bring back the turbo, in the 1978 Buick Regal, followed by the famed Mercedes-Benz 300D and Saab 99 in 1978. The worlds first production turbodiesel automobile was also introduced in 1978 by Peugeot with the launch of the Peugeot 604 turbodiesel.
Renault however give another step and istalled a turbocharger to the smallest and lightest car they had, the R5, making it the first Supermini automobile with a turbocharger. This, combined with an incredible lightweight, gave the car about 230bhp (an exorbitant power for 1400cc) and reach the level of the incredibly fast Ferrari 308. Pontiac also introduced a turbo in 1980 and Volvo Cars followed in 1981.
In Formula 1, in the so called "Turbo Era" of 1977 until 1989, engines with a capacity of 1500 cc could achieve anywhere from 1000 to 1500 hp (746 to 1119 kW) (Renault, Honda, BMW). Renault was the first manufacturer to apply turbo technology in the F1 field, in 1977. The project's high cost was compensated for by its performance, and led to other engine manufacturers following suit. The Turbo-charged engines took over the F1 field and ended the Ford Cosworth DFV era in the mid 1980s.
See also
The most powerful turbo-engined car was the Porsche 917/30 Can-Am, in 1973. Its engine developed 1.100 (or 1.200) hp in race configuration, and a maximum power of 1.560 hp in the qualifying setup.
External links
- turbo.htm How turbochargers work at HowStuffWorks.com
- Autozine Technical School: Forced Induction
- T25 Turbo Information about the T25 turbo series
- T3/T4 Turbo Information about the T3/T4 turbo series